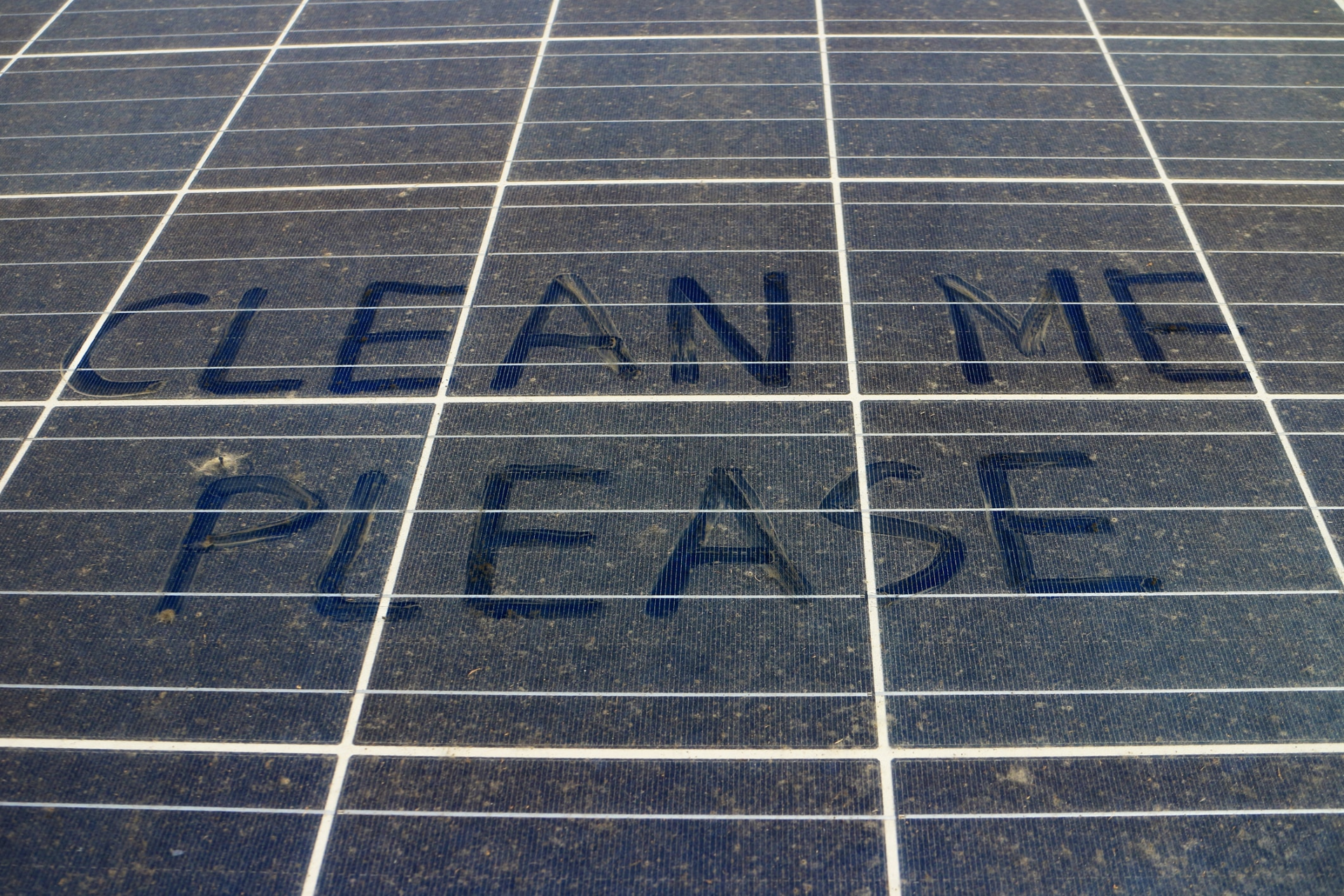
Faurecia Interior Systems case study
Project Summary
- Developed Recruitment plan & process for >250 staff for JIT plant launch
- Trained 250 staff to 100% proficiency in 4 operating stations for plant launch
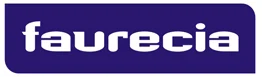
The Challenge
- Delivering a separate design of JIT seating to both Stellantis & BMW from a single production site saw our client facing multiple and conflicting operational challenges on a day-to-day basis. Including coping with a high level of schedule variation resulting in the plant having to manage unbalanced throughput, unstable supplied part availability and increased non-standard handling which resulted in reduced efficiency and variable quality output.
- In addition, two completely new products had to be launched simultaneously, putting further pressure on the already stretched plant team.
The Solution
- Jigsaw provided three senior consultant, specialising in the areas where improvements were required.
- Capacity improvement – Involving change concept of production line & material flow equipment, its industrialisation, line balancing and operational staff training / people upskilling.
- New Product launch – Involved with the creation of OBEYA rooms, rigid short interval change control and stakeholder management of both, local / central customer & client staff, plus close supplier follow up.
- Quality improvement – Included the creation of an enabling data collection technology to accurately record issues
which allowed for improved root cause identification and implementation of more robust containment action with live closed loop feedback to ensure ongoing adherence and repeatability of output Quality.
Why Jigsaw Business Group?
- A proven track record with a team possessing real industry experience, as such, possessing empathy to support businesses accordingly, understanding individual pain points.
- Unrivalled sector knowledge and technical expertise with an ability to look at things from a fresh perspective to deliver process driven solutions that help businesses to reduce costs, increase efficiencies and streamline business operations;
Key Achievements
- Drove data collection and calculations to justify a complete change in plant operating strategy.
- Improved production line capacity / output from 25 > 50 seat sets* per hour over 3-months.
- Management of product quality changed from reactive to proactive identification, containment and implementation of corrective action at source.
- Two new products* being launched on time to customer milestones and targets
- Delivering a separate design of JIT seating to both Stellantis & BMW from a single production site saw our client facing multiple and conflicting operational challenges on a day-to-day basis. Including coping with a high level of schedule variation resulting in the plant having to manage unbalanced throughput, unstable supplied part availability and increased non-standard handling which resulted in reduced efficiency and variable quality output.
- In addition, two completely new products had to be launched simultaneously, putting further pressure on the already stretched plant team.
- Jigsaw provided three senior consultant, specialising in the areas where improvements were required.
- Capacity improvement – Involving change concept of production line & material flow equipment, its industrialisation, line balancing and operational staff training / people upskilling.
- New Product launch – Involved with the creation of OBEYA rooms, rigid short interval change control and stakeholder management of both, local / central customer & client staff, plus close supplier follow up.
- Quality improvement – Included the creation of an enabling data collection technology to accurately record issues
which allowed for improved root cause identification and implementation of more robust containment action with live closed loop feedback to ensure ongoing adherence and repeatability of output Quality.
- A proven track record with a team possessing real industry experience, as such, possessing empathy to support businesses accordingly, understanding individual pain points.
- Unrivalled sector knowledge and technical expertise with an ability to look at things from a fresh perspective to deliver process driven solutions that help businesses to reduce costs, increase efficiencies and streamline business operations;
- Drove data collection and calculations to justify a complete change in plant operating strategy.
- Improved production line capacity / output from 25 > 50 seat sets* per hour over 3-months.
- Management of product quality changed from reactive to proactive identification, containment and implementation of corrective action at source.
- Two new products* being launched on time to customer milestones and targets